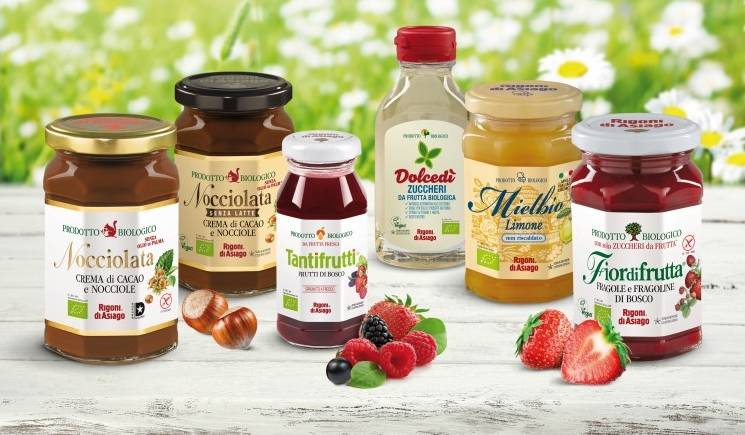
Sfruttare i dati e le informazioni di processo per migliorare la produzione, operare una pianificazione più oculata e ottimizzare l'impiego delle risorse. La storia di innovazione di Rigoni di Asiago.
Dal miele delle origini alle preparazioni a base di frutta, fino alle creme spalmabili, ai dolcificanti e ai nettari: la produzione di Rigoni di Asiago, una realtà che occupa circa 100 dipendenti per un fatturato di 116 milioni di euro, è una delle eccellenze del made in Italy nel settore dell’alimentare e del biologico. Una storia quasi centenaria, per un'azienda a conduzione familiare che fa della qualità (e della tecnologia) il suo punto di forza per distinguersi in un mercato caratterizzato da forte competitività, che abbiamo raccontato per la rubrica "SPS Italia HUB" su Industria Meccanica. La versione integrala è in uscita sul numero di gennaio-febbraio della rivista.
Flessibilità ed efficienza per rispondere alle sfide del mercato
La storia di innovazione di Rigoni di Asiago, raccontata da Silvano Casaro, responsabile Programmazione della Produzione e Tracciabilità del prodotto, è una delle protagoniste della tavola rotonda di Verona intitolata "Food processing 4.0: le tecnologie abilitanti raccontate dai protagonisti del settore": una giornata organizzata da SPS Italia nell'ambito del ciclo di incontri nati proprio per permettere alle eccellenze italiane di condividere esperienze e storie di successo e per diffondere una "cultura 4.0". E quella di Rigoni di Asiago è in effetti una storia davvero emblematica di come anche realtà di consolidato successo non debbano mai smettere di investire in innovazione per raggiungere nuovi traguardi.
Il mondo del food è infatti uno dei comparti che maggiormente avverte la necessità di reagire a un mercato sempre più esigente sia in termini di qualità sia in termini di varietà del prodotto. Rigoni di Asiago si è posta questo problema già da alcuni anni e, dopo un'attenta analisi dei propri processi, ha deciso di rispondere a questa sfida investendo in tecnologia e aggiornando i propri sistemi di gestione della produzione per ottenere maggiore flessibilità ed efficienza.
L'automazione a supporto dei processi decisionali
"Siamo partiti con un'analisi della struttura del nostro processo produttivo", racconta Casaro. "L'azienda ha sempre investito con soddisfazione in automazione. Anche stavolta volevamo capire se queste tecnologie potessero aiutarci a recuperare maggiori informazioni sui nostri processi".
In passato, infatti, Rigoni di Asiago operava un monitoraggio del processo "a posteriori", venendo così a conoscenza di quello che era accaduto quando era ormai troppo tardi per operare i necessari aggiustamenti. "Volevamo disporre di una base dati aggiornata in tempo reale per comprendere meglio quello che accade in produzione e poter così prendere delle decisioni effettivamente basate su informazioni". L'idea è quindi quella di attrezzarsi per interfacciare le macchine con il sistema gestionale, per poter generare un flusso di dati continuo e bidirezionale tra i reparti e gli uffici di pianificazione e controllo.
"Il primo investimento è su un sistema MES (Manufacturing Execution System) specifico per il settore alimentare, che si colloca all'interno del processo e mette così in grado le macchine di ricevere e trasmettere dati". La scelta ricade su un prodotto offerto dalla FB Engineering, customizzato sulla base delle specifiche esigenze di Rigoni di Asiago.
Il secondo step è stato un sistema dedicato al monitoraggio dei consumi energetici. In questo caso la scelta ricade su Aprol EnMon di B&R, fornitore dal quale Rigoni di Asiago acquista anche diversi PC industriali sui quali far girare gli applicativi in grado di dialogare con i diversi PLC posizionati sulle macchine.
Avere a disposizione tutte le informazioni che consentono di comprendere i costi di ciascuna produzione rappresenta uno strumento di indiscutibile utilità per diversi aspetti: "Siamo riusciti a mettere a punto un sistema integrato che ci permette di controllare i processi di produzione, gestire la tracciabilità, governare le fasi di pianificazione, controllare la manutenzione e gestire i consumi di energia, un fattore cruciale per la valutazione dei costi industriali", spiega Casaro.
Una lente d'ingrandimento sui processi produttivi
Le tecnologie acquisite hanno consentito a Rigoni di Asiago di operare un'importante ristrutturazione dei processi. "Siamo partiti dalla definizione dell'anagrafica del prodotto, un aspetto apparentemente banale, ma di assoluta importanza per riconoscere il prodotto nel processo. Poi abbiamo lavorato sulla distinta base di processo, suddivisa nelle tre diverse fasi del nostro processo produttivo: la preparazione della ricetta, cioè la fase in cui si mixano le materie prime, la fase di filling e dosatura del prodotto e infine quella del confezionamento ed etichettatura".
Grazie alle distinte di lavoro e alla creazione di una precisa identità digitale per tutti i centri di lavoro oggi Rigoni di Asiago è in grado di garantire una tracciabilità assoluta di tutte le fasi della lavorazione. "La tracciabilità viene fatta direttamente sulle linee sfruttando sistemi di lettura dei codici. Oggi per ogni fase del processo sappiamo perfettamente chi ha fatto cosa".
Controllo sistematico e continuo del processo
Dal processo vengono estratti in tempo reale i parametri relativi a peso, tempi e temperature dei materiali. "In questo modo sappiamo se si verificano delle deviazioni rispetto agli standard di processo prefissati".
Sono inoltre monitorati e comunicati al sistema gestionale anche i versamenti di produzione, cioè le quantità di prodotto finito che vanno a magazzino.
Grande attenzione è riposta anche alla gestione della manutenzione. Ogni intervento viene accuratamente registrato ed entra così in uno storico che consente di calcolare l'effettiva disponibilità dell'impianto.
Work in progress
Se il grosso degli investimenti per la riorganizzazione dei sistemi di produzione è stato ormai effettuato, la strada dell'innovazione è però un libro ancora tutto da scrivere. "Grazie ai dati che riceviamo dai nostri sistemi non solo impariamo ogni giorno di più a conoscere e governare i nostri processi, ma possiamo anche implementare dei piccoli e continui miglioramenti suggeriti proprio dalle analisi di questi dati". Un esempio? "Abbiamo implementato un sistema di controllo sistematico dell'overfilling dei barattoli. Ricevere i dati in tempo reale consente ai nostri operatori di intervenire tempestivamente per ridurre immediatamente l'eccesso di prodotto sin dal barattolo successivo".
Tag tematici: Made in Italy Manifatturiero SPS Italia
Condividi: