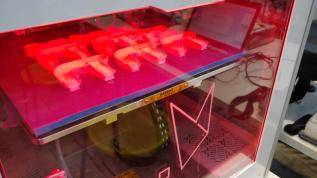
We love our customer we love our future
Innovare non significa solo ideare soluzioni vincenti per il futuro ma anche essere pronti a fornire risposte e soluzioni tecnologiche in caso di emergenza. Con rapidità ed efficacia. Così è accaduto in Leonardo, pronta ad intervenire nel grande fabbisogno di respiratori, presso gli ospedali italiani, generato dall’emergenza Coronavirus.
E’ successo tutto in pochissimi giorni, da quando la società Isinnova di Brescia ha annunciato di aver sviluppato un progetto che prevede la realizzazione, da parte di altre aziende, di valvole in materiale plastico (le cosiddette valvole Charlotte e Dave) che consentono di modificare un particolare modello di maschere subacquee per trasformarle in respiratori destinati alle terapie sub-intensive.
Isinnova, nell’occasione, ha lanciato un appello pubblico per ricevere supporto nella realizzazione di queste valvole per far fronte alle numerose necessità espresse dalla Protezione Civile e da altri enti nazionali e internazionali coinvolti nella gestione di questa emergenza.
Leonardo ha prontamente contattato Isinnova e si è proposta per supportare questa iniziativa che richiede l’utilizzo della tecnologia del cosiddetto additive manufacturing, comunemente noto come 3D printing, per la realizzazione delle valvole. Una tecnologia che Leonardo ha sviluppato, anche attraverso il lavoro svolto all’interno dell’Aerotech Campus di Pomigliano d’Arco (il primo dei Leonardo Labs recentemente inaugurato), e che trova in questi giorni piena applicazione presso il sito di Grottaglie, in Puglia, specializzato in tecnologie avanzate per la produzione di parti di aereo in fibra di carbonio.
Ma non solo: sullo stesso fronte si è messa subito al lavoro anche la divisione Elettronica di Leonardo, che presso i propri stabilimenti di La Spezia e Livorno, ha analogamente raccolto l’iniziativa intrapresa dalla società Isinnova di Brescia. Quest’ultima, infatti, ha reso disponibile, anche in questo caso, i disegni costruttivi della valvola e di un secondo raccordo accessorio, consentendo al reparto Ingegneria di realizzare un primo Kit con la stampa 3D e di testarlo con successo su una maschera da snorkelling.
Tornando al sito di Grottaglie, in pochi giorni è stata lanciata la produzione dei primi lotti di valvole (sono già stati realizzati oltre 200 kit di valvole) per supportare le necessità insieme ad una valutazione più estesa delle potenziali applicazioni delle proprie tecnologie a supporto della Protezione Civile e delle Regioni nella crisi provocata da Covid-19. Tra queste rientra la possibilità di una produzione massiva di dispositivi medicali come, per esempio, le maschere Face Shield, i cui primi prototipi in stampa 3D già sono stati realizzati presso l’area di Ricerca e Sviluppo del sito di Grottaglie.
Da segnalare inoltre che Leonardo è in contatto anche con altre aziende che producono respiratori polmonari per terapia intensiva, per la realizzazione, sempre in additive manufacturing, di componenti dei respiratori polmonari e per altre analoghe esigenze.
Come si realizza la valvola Charolette in 3D Printing
Il processo inizia con la realizzazione a CAD in modello 3D della valvola che diventa un file di scambio con cui ‘istruire’ la stampante. Successivamente una testina a controllo numerico deposita un filamento termoplastico secondo la geometria prestabilita nel file di scambio.
Questo processo viene realizzato in temperatura e il successivo raffreddamento consegna il componente stampato 3D alla finitura finale. Per le valvole Charlotte e Dave sono stati utilizzati diversi materiali: è stato privilegiato il PLA (Acido Polilattico) che è tra i più economici e comunque sufficientemente idoneo per caratteristiche strutturali. Inoltre il PLA è biocompostabile.
Segui Leonardo su Twitter, LinkedIn e Instagram per seguire le iniziative che sta mettendo in campo a sostegno di chi sta lavorando per il contenimento del contagio da Covid-19.
Tag tematici: Additive Manufacturing Covid-19 Networking Stampa 3D
Condividi: