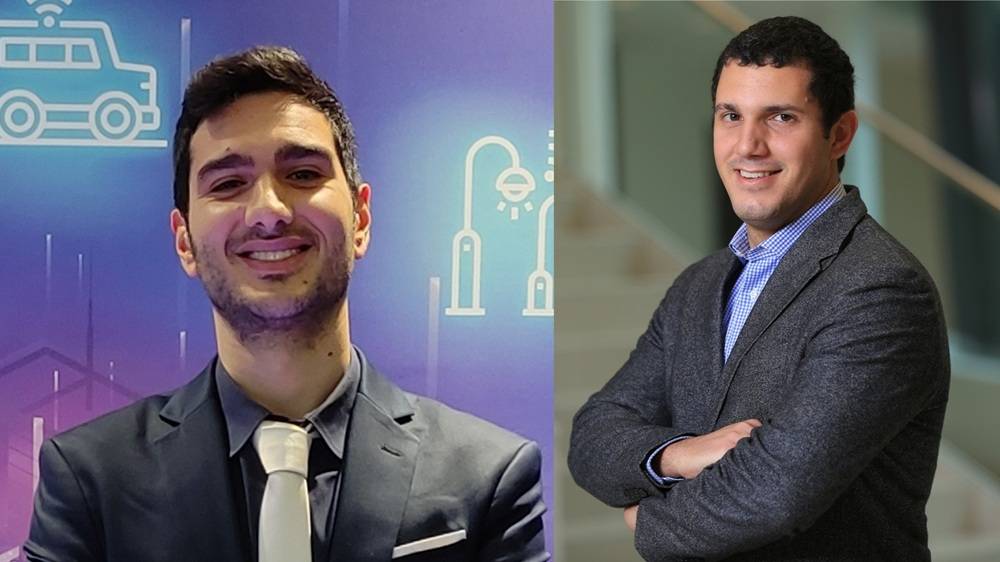
Intervista a Niccolò Spinola, Software Driven automation Product Manager – Digital Industries di Siemens e Giuseppe Morabito, Industrial Edge Ecosystem Product Manager – Digital Industries di Siemens.
Siemens sta puntando molto sul ruolo delle tecnologie digitali come fattori abilitanti per un futuro sostenibile. Qual è, dal vostro punto di vista, il legame tra digitale e sostenibilità?
La sostenibilità è profondamente integrata nelle nostre attività di business, incluse le scelte di investimento e di governance. Questo profondo impegno a 360° si traduce anche nell'ampio programma denominato DEGREE, che rappresenta il vero DNA della nostra azienda. Siamo una società altamente tecnologica, con un portafoglio disegnato per guidare una trasformazione digitale e sostenibile del mondo industriale e delle infrastrutture. Il nostro portafoglio di tecnologie digitali garantisce trasparenza dei dati e ottimizzazione della produzione, aumentando l'efficienza energetica e delle risorse per creare prodotti e processi di produzione sostenibili. Grazie a queste soluzioni tecnologiche, nate dall'integrazione unica tra reale e virtuale, alle nostre competenze esclusive e al nostro approccio strategico, mettiamo i nostri clienti nelle migliori condizioni per massimizzare il loro contributo nella società.
Che cosa intendete quando parlate di Industrial AI e quali sono i benefici offerti dall'integrazione dell'intelligenza artificiale nell'automazione industriale?
(NS) Quando parliamo di Industrial AI intendiamo proprio l’adozione dei modelli di Machine Learning al mondo dell’automazione industriale allo scopo di ottenere benefici pratici. Sebbene a prima vista l’applicazione di tali tecnologie possa sembrare del tutto naturale, nella realtà, come avviene per gran parte delle metodologie IT, è necessario tenere conto delle peculiari caratteristiche del mondo OT. I requisiti di funzionamento, sicurezza e gestione dei dati nell’automazione è infatti molto diverso e necessita di una standardizzazione differente che tenga conto di processi strutturati per lo sviluppo delle applicazioni (MLops) costruiti appositamente per essere inclusi nei cicli di controllo degli impianti industriali portando un effettivo valore aggiunto, specie dove tocca operare, come spesso capita, in situazioni di “brownfield” e, pertanto, con maggiore delicatezza. Inoltre, la gestione dei dati è un punto critico in questo scenario perché non sono liberamente disponibili e utilizzabili come negli ambiti classici dell’IT o nell’intelligenza artificiale generativa, ma devono spesso essere ottenuti mediante elaborazioni dedicate e richiedono un livello di protezione a più livelli.
I benefici sono la chiave dell’adozione dell’Industrial AI in questo panorama e coinvolgono in realtà tutta la catena del valore a partire dalla progettazione dei sistemi fino alla gestione dei servizi correlati. Ne consegue un generale miglioramento della qualità del lavoro e la riduzione dell’expertise richiesto risolvendo la cronica mancanza di lavoratori specializzati, allo stesso tempo ottenendo la possibilità di integrare la propria offerta con nuovi servizi che possono essere sfruttati dagli utilizzatori per migliorare la produzione ad ampio raggio. Infine, questi strumenti permettono anche di poter estendere il range di applicazioni dell’automazione industriale permettendo di inserirsi in ambiti che erano primi preclusi per l’eccessiva complessità che ora l’Industrial AI è in grado di risolvere con grande efficienza.
Che legame c'è tra le soluzioni software per la progettazione e la simulazione e il "metaverso industriale"?
(NS) Il Metaverso industriale ha una correlazione molto forte con la progettazione e la simulazione ma si tratta, fondamentalmente di un concetto diverso e innovativo. Da questo punto di vista è importante comprendere la differenza fra simulazione e virtualizzazione che, sebbene abbiano in comune l’idea di ripetere nel mondo digitale delle operazioni che dovrebbero avvenire nel mondo fisico, sono diversi. La simulazione si basa specificamente sull’idea di un modello della realtà che si sostituisce in toto ad essa e diventa immutabile. La virtualizzazione, invece, vuole creare una vera e propria rappresentazione fedele della realtà, in tutte le sue componenti, come l’ambiente esterno ed anche, non in ultimo, dell’hardware fisico che viene utilizzato. Ad esempio, è possibile simulare il comportamento aerodinamico di un’automobile in base alla sua forma e alle condizioni al contorno. Ma se si vuole creare un gemello digitale dell’automobile non ci si può limitare al suo comportamento aerodinamico ma di concerto devo essere in grado di riprodurre il comportamento di tutti i suoi componenti. Questo gemello digitale ora non è più una semplice simulazione perché nel metaverso può essere inserito in molteplici contesti (come crash test virtuali o perfino competizioni con altri veicoli virtuali) messi a disposizione dall’ambiente del metaverso il quale a sua volta viene creato per riprodurre il comportamento fisico di un ambiente reale. Lo stesso concetto lo posso applicare a un macchinario industriale o ad un’intera linea di produzione arrivando, volendo, a ricreare un’intera fabbrica.
Il Metaverso è quindi un vero e proprio ecosistema aperto che facilita in maniera estrema la collaborazione fra terze parti. Nel mondo dell’automazione, infatti, una delle difficoltà principali può essere il mettere assieme sistemi di provenienza diversa, magari pensati per applicazioni diverse e gestirli in un’applicazione nuova per creare innovazione.
Questo è estremamente dispendioso nella realtà ma in un mondo virtuale invece è possibile utilizzare i Digital Twin on modo da poter provare infiniti scenari e risparmiando tempo e risorse perché le configurazioni diventano di immediato utilizzo e facilmente gestibili nonché riutilizzabili a piacere. Di conseguenza il Metaverso può essere utilizzato per l’implementazione software di progettazione e per la simulazione ma è in grado di lavorare ad un livello superiore. Ad esempio, vi posso inserire i dati della produzione “fisica” reale per vedere come questi interagiscono nella realtà virtuale con lo scopo di prendere poi decisioni che posso applicare direttamente nel mondo virtuale ma valgono allo stesso modo nel mondo fisico e reale.
Quali sono gli utilizzi concreti dell'Industrial Edge per OEM ed End User?
(GM) Gli OEM possono equipaggiare i loro prodotti con app Industrial Edge per proporre servizi a valore aggiunto che estendono le funzionalità delle macchine e che permettono di analizzare il funzionamento dei macchinari anche dopo la consegna al cliente. Inoltre, gli aggiornamenti software possono essere eseguiti da remoto e a livello centralizzato, abilitando così gli OEM a una gestione più efficiente delle loro commesse. Tutto questo porta a una riduzione dei costi di service, a un time-to-market ridotto e a una maggior qualità del servizio offerto al cliente.
D'altro canto, gli end user che sfruttano Industrial Edge hanno accesso facilitato ai dati di produzione e introducono nei loro impianti nuove features che aiutano a ridurre il numero di scarti, errori e downtime inattesi, avvalendosi ad esempio di applicazioni di manutenzione predittiva per la rilevazione precoce di anomalie. Altre applicazioni ampiamente diffuse tra questo tipo di clienti sono il monitoraggio dei parametri di produttività nonché dei consumi energetici, che consentono di raggiungere anche obiettivi in termini di sostenibilità, oltre che di riduzione costi.
Tag tematici: Interviste e Editoriali
Condividi: